In the fast-changing world of manufacturing, Artificial Intelligence (AI) is proving to be a game-changer. AI isn’t just streamlining production lines, it’s also making quality control sharper and driving efficiency through the roof. At Simelabs, we’re leading this charge with our innovative product, a solution that’s already making waves, particularly in pharmaceuticals where precision and quality are paramount.
Unleashing AI Power in Manufacturing
Artificial Intelligence (AI) has emerged as a cornerstone of modern manufacturing, revolutionizing the industry with its advanced capabilities and transformative impact. Its ability to process and analyze vast amounts of data in real time has fundamentally changed how manufacturers operate, enabling them to make well-informed decisions and optimize their production processes more effectively than ever before.
One of the most significant advantages of AI in manufacturing is its integration with the Internet of Things (IoT) to facilitate real-time data acquisition. IoT devices embedded throughout the production process continuously capture data from various points, such as machinery, raw materials, and final products. This real-time data collection provides manufacturers with a comprehensive view of their operations, allowing them to monitor every aspect of production closely. For instance, sensors placed on production lines can track machine performance, while data from quality control tests can be fed directly into AI systems for immediate analysis. By providing a granular view of the production process, AI helps manufacturers identify inefficiencies, detect issues early, and make informed adjustments to improve overall performance.
Predictive analytics is another powerful feature of AI that offers significant benefits to manufacturers. AI models leverage historical data to forecast potential failures and anomalies before they actually occur. This proactive approach is crucial for minimizing operational disruptions and preventing costly downtime. For example, by analyzing patterns in historical production data, AI can predict when a machine is likely to fail or when a batch of products might not meet quality standards. This foresight enables manufacturers to implement preventive measures, such as scheduling maintenance or adjusting production parameters, to address issues before they escalate. As a result, manufacturers can maintain smooth and efficient operations, reduce unplanned downtime, and improve the overall reliability of their production processes.
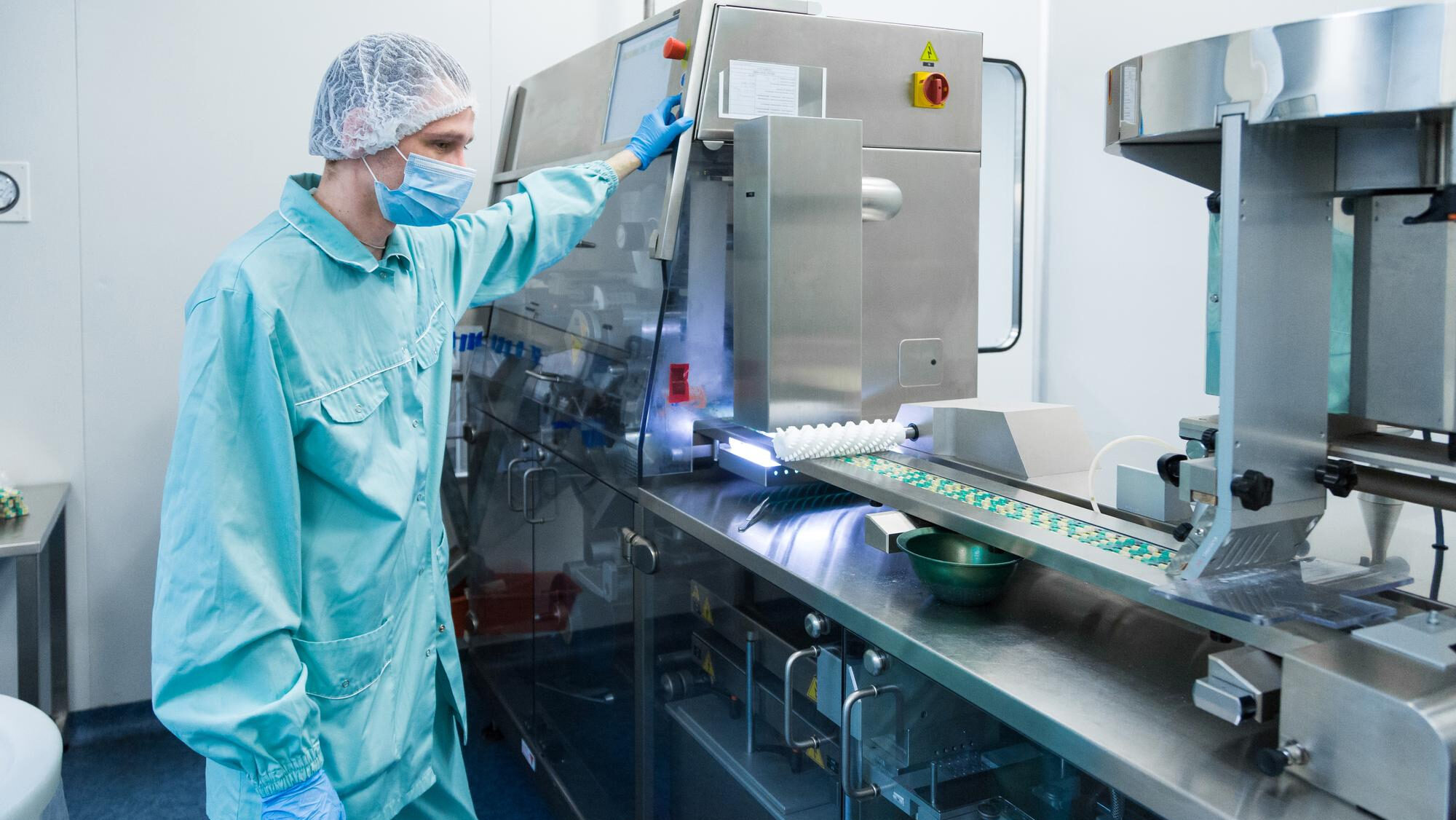
Moreover, AI plays a crucial role in ensuring the security and integrity of data exchanged across various departments within an organization. In a manufacturing setting, data security is paramount, as sensitive information related to production processes, quality control, and supply chain management must be protected against unauthorized access and tampering. AI systems, combined with advanced security technologies, provide secure and tamper-proof data exchange mechanisms. For instance, blockchain technology can be integrated with AI to create an immutable ledger of production data, ensuring that information remains accurate and trustworthy throughout its lifecycle. This secure data exchange fosters trust among different departments, facilitates compliance with regulatory standards, and enhances overall organizational efficiency.
AI’s impact extends to process optimization, where it plays a vital role in streamlining manufacturing operations. By analyzing trends and identifying outliers in production data, AI provides valuable insights that help manufacturers optimize their processes. For example, AI algorithms can detect deviations from normal operating conditions, such as variations in product quality or unexpected changes in machine performance. These insights enable manufacturers to take corrective actions and refine their processes to achieve greater efficiency and productivity. In industries like pharmaceuticals, where precision and quality are of utmost importance, AI’s ability to enhance process optimization is particularly beneficial. AI-driven process optimization not only improves product quality but also drives innovation by uncovering new opportunities for process improvements and operational enhancements.
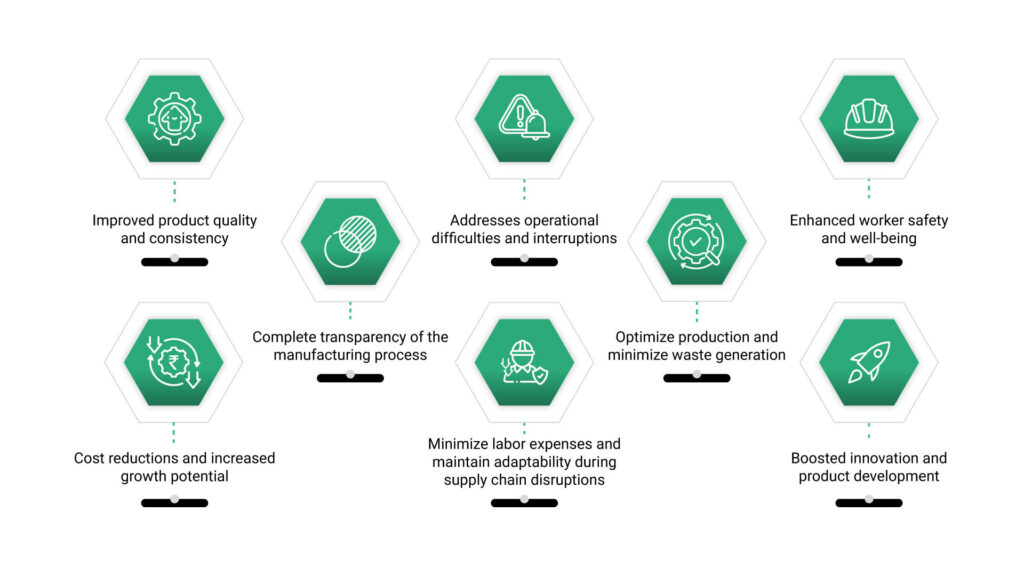
A Breakthrough in Pharma Manufacturing
How Simelabs’ Edge XY is Setting New Standards
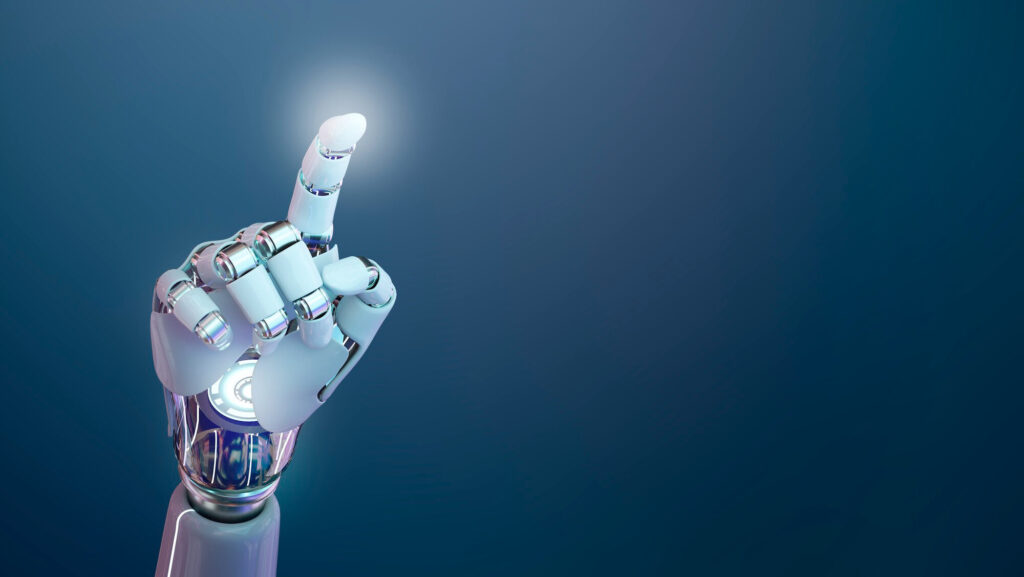
In a significant advancement for the pharmaceutical industry, Simelabs has pioneered a cutting-edge solution leveraging Artificial Intelligence (AI) to revolutionize manufacturing processes. This solution specifically addresses critical challenges faced by pharmaceutical manufacturers, with a particular focus on enhancing quality control and optimizing resource management.
The core innovation lies in the solution’s ability to harness AI for the meticulous extraction and analysis of quality information from raw materials. This ensures that only the highest-grade inputs are used in production, thereby significantly mitigating the risk of wasted batches and ensuring product consistency. Furthermore, the solution incorporates Internet of Things (IoT) technology to capture process data in a standardized format. This comprehensive data capture provides a granular view of the entire manufacturing process, empowering manufacturers with unparalleled precision in monitoring and controlling every production stage.
To further elevate process optimization, the solution features a sophisticated dashboard that visualizes trends and normalcy studies. This translates to clear and actionable insights for manufacturers, enabling them to identify patterns and anomalies with greater ease. Proactive intervention becomes possible through the solution’s AI-powered prediction of batch failures, allowing for timely adjustments and a significant reduction in the likelihood of quality issues.
Simelabs’ commitment to data security is evident in the solution’s secure data exchange capability. By leveraging blockchain technology, the solution ensures that data exchanged across departments is tamper-proof and completely secure. This not only enhances compliance with relevant regulations but also fosters trust and transparency among all stakeholders within the organization.
How edge XY Addressed Pharmaceutical Manufacturing Challenges
A persistent challenge within the pharmaceutical industry lies in the failure of chemical compound batches to meet stringent quality control standards. These failures result in significant resource wastage, impacting everything from raw materials and production time to lab personnel and operational costs. To address this critical issue, a novel AI-powered solution has emerged, offering a paradigm shift in pharmaceutical manufacturing.
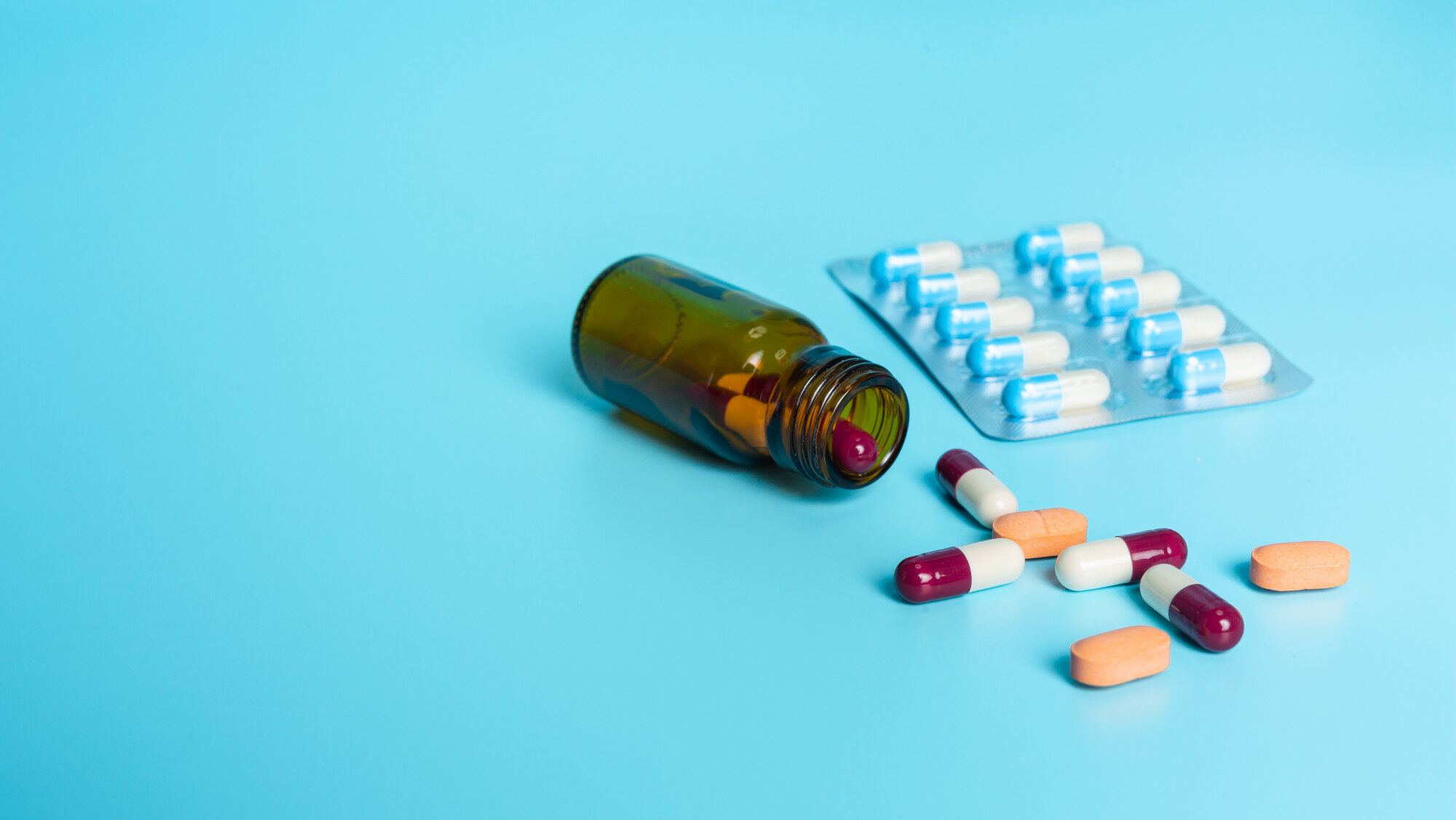
This advanced solution leverages the power of Machine Learning, a subfield of AI, to analyze vast amounts of historical data. By meticulously examining past production cycles, the solution can identify patterns and subtle anomalies that might foreshadow potential quality failures in future batches. This predictive capability empowers manufacturers to take a proactive approach, intervening before issues arise and preventing wasted resources. The benefits extend far beyond mere waste reduction. Early detection of potential failures, facilitated by real-time data extraction, translates to minimized downtime and streamlined operations. Imagine a scenario where quality control concerns are identified and addressed before they snowball into production delays. This translates to significant cost savings and improved overall efficiency.
Furthermore, the solution delves deeper by providing detailed root cause analysis for batch failures. This granular level of insight allows manufacturers to pinpoint the exact source of the problem, enabling them to implement targeted corrective measures and prevent similar issues from recurring in the future. But the impact doesn’t stop there. The solution fosters a holistic view of the manufacturing process by aggregating data from multiple departments. This comprehensive data picture empowers cross-functional collaboration and coordination, ensuring all stakeholders are aligned and working towards a common goal – consistent, high-quality production.
The positive outcomes culminate in a demonstrably more streamlined and efficient manufacturing operation. By optimizing processes and minimizing failures through AI’s predictive capabilities, the solution paves the way for increased productivity and cost savings. This represents a significant step towards Industry 4.0, a vision of interconnected, intelligent manufacturing powered by advanced technologies like AI, IoT (Internet of Things), and secure data exchange.
In essence, this innovative AI-powered solution tackles the challenge of quality control head-on, transforming the landscape of pharmaceutical manufacturing from a reactive to a proactive approach. It empowers manufacturers to optimize processes, minimize waste, and ultimately deliver high-quality products with greater efficiency.