In today’s fast-evolving industrial landscape, businesses are increasingly turning to innovative technologies to enhance workforce training and operational efficiency. Among these advancements, Augmented Reality (AR) and Virtual Reality (VR) have emerged as game-changers, offering immersive and interactive training experiences that go beyond traditional methods.
The Need for Advanced Industrial Training Solutions
Industries such as manufacturing, oil & gas, automotive, and healthcare face unique challenges in training their workforce. Traditional training methods, which often involve classroom-based learning and on-the-job training, can be time-consuming, costly, and sometimes risky. AR and VR provide a safer, more efficient, and cost-effective solution that helps workers acquire hands-on experience in a controlled virtual environment before stepping into real-world scenarios.
How AR and VR Transform Industrial Training
One of the primary advantages of VR in industrial training is the ability to provide fully immersive environments. Trainees can practice complex procedures in a risk-free setting, allowing them to gain hands-on experience without the pressure of real-world consequences. For example, in the oil and gas industry, workers can simulate high-risk operations such as equipment maintenance or emergency response, reducing potential hazards while enhancing skill development.
On the other hand, AR offers real-time guidance by overlaying digital information onto the physical world. Workers can receive step-by-step instructions and visual cues while performing tasks, leading to improved accuracy and efficiency. In manufacturing settings, AR can be used to guide assembly line workers through intricate processes, minimizing errors and optimizing production workflows.
Implementing AR/VR-based training programs also contributes to significant cost savings. By shifting training from live environments to virtual simulations, companies can avoid shutting down production lines, reducing downtime and operational disruptions. This approach leads to lower training costs by eliminating expenses related to travel, equipment wear and tear, and trainer fees.
Another key benefit of AR and VR technologies is their ability to standardize training programs. Regardless of geographic location, employees can access the same high-quality training experience, ensuring consistency in skill levels and operational standards across an organization. This helps businesses maintain quality control and regulatory compliance while fostering a culture of continuous learning.
Additionally, AR/VR training solutions provide valuable data-driven insights for organizations. By tracking trainees’ performance, companies can identify skill gaps, monitor progress, and tailor training programs to individual needs. This data-centric approach enhances workforce competency and prepares employees for future challenges.
Case Study
Immersive VR Training for Precision Manufacturing
At Simelabs, we have successfully implemented AR/VR training solutions for various industries, including the medical equipment sector. One such project involved developing a Virtual Reality training program for operators working with machinery used in the production of critical medical equipment, such as pliers and stoppers. This innovative training solution leveraged immersive VR simulations to enhance operational efficiency, improve safety, and ensure precision in manufacturing processes.
The VR training program featured lifelike 3D models of production machinery, enabling operators to engage in hands-on learning without the constraints of a physical environment. Through interactive modules, trainees were able to practice operating, troubleshooting, and maintaining complex equipment in a virtual setting. The program provided a risk-free environment, eliminating the safety hazards associated with live machinery training.
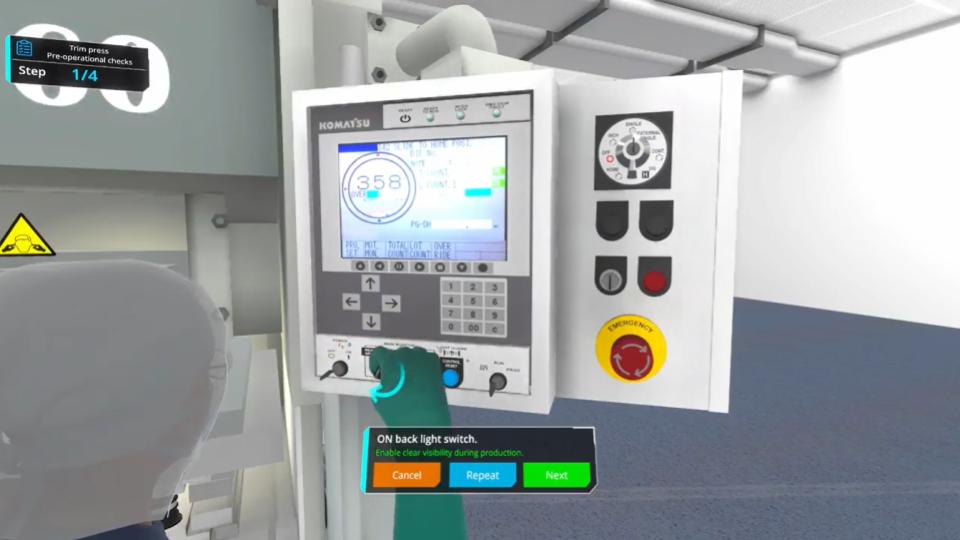
Furthermore, the VR training solution incorporated performance tracking capabilities, offering real-time feedback and assessments to enhance learning outcomes. By monitoring trainees’ progress, the system helped identify areas for improvement and allowed for personalized training experiences. The solution addressed key challenges faced by WEST Pharma, which required a consistent and effective training approach to overcome operational costs, safety risks, and limited equipment availability during live production.
The VR training program was developed for multiple platforms, including Oculus Quest 2, PC, iOS, and Android, ensuring accessibility and flexibility for trainees across different locations. By adopting this innovative solution, WEST Pharma was able to eliminate risks associated with live machinery training, accelerate the learning curve for operators, and reduce downtime and operational costs linked to training on physical equipment.
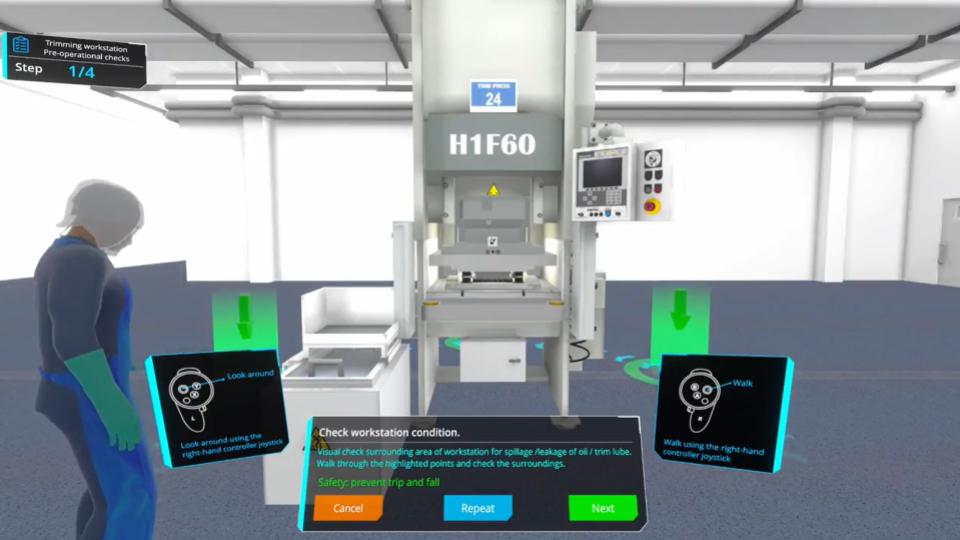
To develop this cutting-edge solution, ASTEK utilized a range of advanced technologies, including VR, Photon, Unity 3D, AWS, 3DS Max, and Maya. Our expertise in these technologies allowed us to create an immersive and effective training experience tailored to the specific needs of our client.
Challenges and Future Prospects
Despite the numerous benefits of AR/VR training, organizations may encounter challenges such as high initial investment costs, content development complexities, and the need for specialized hardware. However, advancements in AR/VR technology, including more affordable and lightweight headsets, cloud-based training platforms, and AI-driven personalization, are making these solutions increasingly accessible and scalable.
As technology continues to evolve, the future of industrial training with AR/VR looks promising. Businesses that embrace these innovations will gain a competitive edge by enhancing workforce efficiency, reducing training-related costs, and fostering a safer working environment.
AR and VR technologies are revolutionizing industrial training by providing immersive, safe, and cost-effective learning experiences. As businesses strive to upskill their workforce and stay competitive, embracing AR/VR-based training solutions can lead to improved efficiency, reduced risks, and higher employee engagement.
At Simelabs, we specialize in developing AR/VR training solutions tailored to your industry’s needs. Whether you are looking to enhance operational efficiency or improve workforce safety, our expertise can help you achieve your training goals.
Contact us today to explore how we can support your digital transformation journey.
The industrial sector is at the cusp of a digital revolution, and those who invest in AR/VR training today will be well-positioned to navigate the challenges of tomorrow. Are you ready to take the leap?